Breaking Silos, Boosting Efficiency: The Transformative Power of MES Centers of Excellence
By Francisco Almada Lobo, CEO at Critical Manufacturing, Industry 4.0 Evangelist and Educator
In the complex and dynamic world of global manufacturing, companies operating multiple sites often deal with considerable challenges. Each plant within these enterprises may come with its own unique set of systems, whether commercial, custom, or legacy, often as a result of distinct historical paths and acquisitions.
Additionally, the disparity in product lines and manufacturing processes across these plants creates a complex matrix that can hinder unified corporate progress. The implementation of a Manufacturing Execution System (MES) Center of Excellence (CoE) offers a strategic solution, aiming to standardize processes and technologies across these diverse environments while fostering agility and responsiveness to shifting business conditions.
This article only intends to lift the veil on some of the main aspects to take into consideration when establishing a CoE, and just scratches the surface of the topics. For a more detailed analysis, make sure to read the white paper written by João Cortez on the subject.
The Rationale Behind an MES Center of Excellence
Integrating an MES across various manufacturing sites is a substantial undertaking that requires significant investment and coordination. For enterprises with multiple locations, individually tailored MES implementations can lead to unsustainable costs and fragmented systems. Establishing a corporate MES baseline provides a critical opportunity not only to standardize and optimize processes but also to harmonize operations across all sites, leveraging economies of scale.
A particularly crucial aspect of implementing a CoE is the drastic increase in the speed at which new MES solutions can be deployed across multiple factories. Consider a hypothetical company with 80 plants; attempting to deploy disparate MES projects without any central coordination or synergy between factories could become a logistical nightmare. If each deployment, even when optimized, takes six months, completing the digital transformation for all sites would take an astounding 40 years—a timeframe that makes the urgency and efficiency of a CoE not just beneficial but essential.
By streamlining the deployment process through a CoE, companies can rapidly roll out new technologies, reduce duplication of effort, and ensure that improvements in processes and technologies are swiftly standardized across all facilities. This coordinated approach not only speeds up the overall transformation but also enhances the scalability and flexibility of manufacturing operations, making it easier to adapt to new market demands and changes in production needs.
It is equally important to consider that, as in other enterprise applications, such as ERP or PLM, only part of the business value is achievable with the initial deployment, especially given the complexity and effort required for the necessary changes in the organization, and the organization itself. learning that is being done and that must be incorporated in subsequent releases, in a logic of continuous improvement. In other words, the real value is not reached in the first instance, but the rest of the value generally comes later, as the company learns how to take advantage of the new system’s capabilities.
This means that the CoE not only has to worry about the initial deployments for all factories, but also thinks about the permanent updating of all installed systems.
What If No CoE is in Place?
Neglecting to establish an MES Coe can lead to several significant challenges. Each site operating with its own standards can result in inefficiencies and errors. Without centralized negotiation and purchasing, companies miss out on bulk buying advantages and favorable licensing terms, leading to higher overall costs. A lack of a unified system restricts the flow of information and best practices, which slows down innovation and problem-solving across the enterprise. Varied challenges and inefficiencies in site-specific implementations can cause project delays and decrease the overall return on investment. Furthermore, a disjointed approach to MES can severely limit a company’s ability to respond swiftly to market changes and technological advancements.
The Complexity of Stakeholder Engagement in MES Integration
Successful MES integration within a CoE framework involves multiple stakeholders. Vendors are crucial as they supply the MES software and support, offering continuous updates and customization to meet enterprise-wide needs. System integrators play a pivotal role in ensuring that the MES software integrates seamlessly with existing systems across sites, customizing and deploying the MES according to specific site needs while maintaining a baseline standard. Customer organizations, which include various departments within the manufacturing enterprise such as IT, operations, and quality control, each bring specific requirements and expectations to the MES solution.
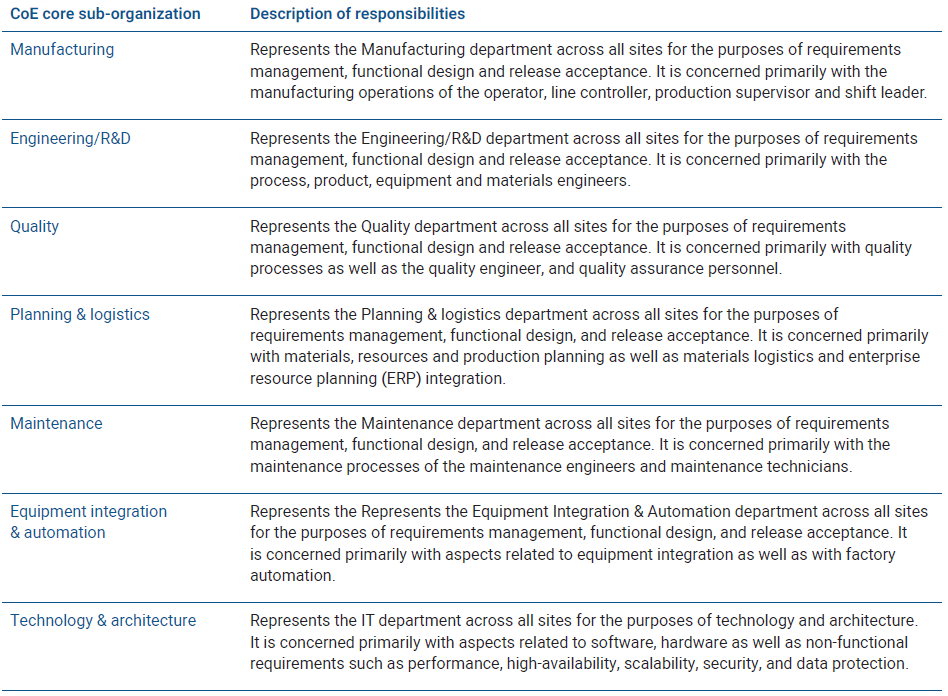
Effective communication and collaboration among these stakeholders are vital for the successful implementation of an MES CoE. Regular meetings, clear communication channels, and established protocols for feedback and adjustments help ensure that the system meets the diverse needs of all parties involved. Additionally, training and support provided by the CoE can empower local teams at each site to make the most of the new systems, ensuring a smooth transition and ongoing operational efficiency.
Flexible Models for MES Centers of Excellence
The operational models for an MES CoE can vary significantly depending on the specific needs and structure of the organization. Some companies may opt for a highly centralized model where a single MES baseline is deployed across all sites. This model offers the highest level of standardization and is typically easier to manage and maintain.
Alternatively, organizations with sites that have similar manufacturing processes might cluster these sites together under a common MES baseline that addresses shared characteristics and needs, while still allowing for some site-specific customizations.
On the more decentralized end of the spectrum, the central part of the MES model within the CoE could be smaller, providing a core set of functionalities while granting individual factories greater flexibility to adapt and extend their MES implementations to meet unique operational demands. This model is particularly useful for companies with highly diverse manufacturing processes or where local compliance and operational conditions vary significantly.
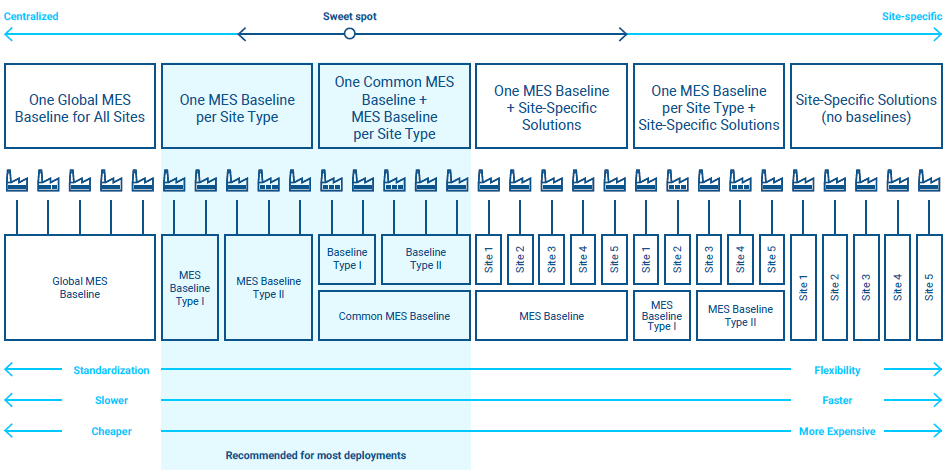
Each model has its advantages and potential challenges, and the choice of model will depend on the specific operational, strategic, and financial goals of the organization. The ability to customize the CoE approach allows for tailored solutions that can accommodate the unique characteristics of each site while maintaining overall coherence and alignment with corporate objectives.
Strategic Recommendations for Implementing an MES CoE
Executive Sponsorship and Strategy Communication
A successful CoE must be championed by a team of corporate executive sponsors. These leaders are essential for articulating the CoE strategy and securing buy-in across various sites. Their support legitimizes the initiative and helps mobilize resources, ensuring that the MES implementation aligns with the broader business objectives and gains the necessary momentum.
Communication, Coordination, and Site Involvement
Effective communication and coordination between the CoE and the different sites are key to the successful deployment and operation of an MES. Regular updates, clear lines of communication, and collaborative problem-solving sessions ensure that all parties remain aligned and engaged. It is also vital that sites are not merely passive recipients of the MES system but are actively involved in the activities. Direct representation of the sites in the CoE organization and giving them ownership of deployment projects enhances their commitment and responsiveness to the initiative.
Agility and Flexibility in Implementation
The CoE and the baseline MES must be agile enough to swiftly address the specific requirements of each plant. While standardization is a primary goal, the MES must also offer sufficient flexibility so that sites can tweak and adjust the system to fit their unique operational needs without deviating from the overall corporate standards.
Application Lifecycle Management (ALM)
Implementing a robust Application Lifecycle Management (ALM) system is crucial. ALM supports the entire lifecycle of the MES from requirements management, through release planning and design, to development, testing, deployment, and ongoing support. This system ensures that updates, upgrades, and changes are managed systematically and efficiently, minimizing disruptions and maintaining system integrity across all sites.
Conclusion: The Strategic Imperative
The establishment of an MES CoE is crucial for manufacturing companies with multiple sites looking to streamline operations and enhance efficiencies. While it requires significant upfront investment in terms of planning, stakeholder engagement, and resource allocation, the long-term benefits include substantial cost savings, improved standardization, and enhanced competitive edge.
By adopting a strategic approach to MES implementation, companies can overcome the complexities of diverse operational environments, fostering a cohesive and innovative manufacturing network. With different operational models to choose from, organizations can tailor their MES CoE to balance centralization with site-specific flexibility, ensuring that the system meets both global standards and local needs.
This approach not only accelerates the deployment of new technologies but also significantly shortens the digital transformation journey across the enterprise.