Design for Sustainability: Consider the End at the Beginning

By Peter Smith, Director of Engineering Solutions, Plexus Corp
80% of all product-related environmental impacts are determined during the design phase of a product. This statistic from the European Council is evidence of the growing need to ensure sustainability is considered across all aspects of design, not just at the end of life. Many factors should be evaluated when reviewing the sustainability or environmental impact of a product. Making informed design decisions means considering supply chain, feasibility or cost and production.

Peter Smith
To compete in the current market, companies must produce complex, high quality products at the optimal cost, while simultaneously meeting customer demands. In order to achieve this, more and more manufacturers are using methods that link the design of a product and process to cost, quality, efficiency and logistics. Different “Design for X” concepts such as “Design for Manufacturability” provide huge opportunities for manufacturers and give them a competitive edge when supporting their end customers.
By employing “Design for Excellence” methodology at the earliest stages of product development, it is possible to improve product designs in terms of supply chain, material cost and automation process in manufacturing. Adding a focus on sustainability at the heart of each of these areas will create a better, more environmentally responsible product – with an end of life plan.
Design for Sustainable Supply Chain
Design for Supply Chain (DfSC) refers to the need to consider the cost and impact of the components/materials selected, the manufacturability and the ongoing capability of the supply chain to scale to required levels and deliver a stable and sustainable supply to meet customer demand. By considering supply chain in the design stage, scalability can be prioritized, limiting potential future procurement delays or costs.
To meet desired expectations for sustainability, how components are sourced must also be considered, i.e. are there local options available to limit environmental impact by reducing shipping distances? Are the components sourced from suppliers with high ethical standards in line with international norms and standards, including the Universal Declaration of Human Rights, ILO International Labor Standards and OECD Guidelines for Multinational Enterprises? Is there any potential to alter the manufacturing processes to produce the components or packaging used to reduce environmental impact?
A high-performing supply chain will have resilience and responsibility at its heart. To accomplish this, supply chain experts must continuously work closely with engineers to identify opportunities for supply chain optimization in the design stage.
Design for Cost & Impact
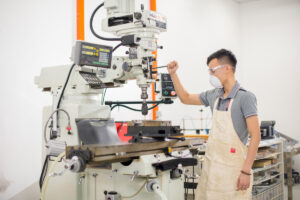
Plexus Engineering Lab
Challenging an engineering team’s design and ensuring sourcing is thoroughly explored helps limit the cost and impact of the final product. Manufacturers have always had to consider cost. Traditionally, impact was generally considered after the design stage: first the product was designed, then it was priced. If the generated design proved too costly, engineers would have to redesign to a new cost target.
A Design for Cost (DfC) approach can also improve the sustainable manufacturability of a product or part. For example, an aluminum frame extrusion that was too heavy would have extremely tight tolerances. This is where ‘lightweighting’ is not just a more sustainable option for plastics or packaging, but many other materials as well. Working through DfC with a recent partner resulted in a 22% decrease in weight – and improved flatness optimizing quality, repeatability and cost reduction – ultimately using less resources. Various questions should be asked during the design process, such as: Is there an ability to merge parts to result in fewer parts and/or processes to thereby reduce cost and impact? Can we change the finish? Only if all possibilities are considered and evaluated early can manufacturers deliver each product to market with full functionality at lower impact.
Today, engineers have a responsibility to consider not only the cost of manufacture, but also the impact and end of life of a product. How will a product be disposed of? Can components be recycled or sold for reuse? Does the product hold value at the end of its life, or is it a financial and environmental burden to dispose of? These considerations should be part of design and support a design that limits the cost and end of life impact of a product.
Design for Automation
Many manufacturers focus on getting production up and running before they turn their attention to automation. But this approach can have inherent challenges – like when a manufacturer discovers the product isn’t compatible with its automation systems, resulting in costly and wasteful changes. Design for Automation (DfA) can help prevent these problems and make a smooth transition from prototype to production. Automation is a huge opportunity for improving the sustainability of a product, limiting waste, increasing the efficiency of production and for ensuring less energy use than some manual production.
With a DfA approach, product designers and production engineers work together and plan for automation in the initial design phases of the product. First, product designers develop parts often using rapid prototyping technology, such as 3D printing technology. Then, the production engineers scrutinize the ability of their automation system to see, pick and place those parts. This approach allows the two teams to identify any gaps between a product’s design and the automated production of that design. If a production issue is discovered, the production team can give suggestions to the design team to develop a solution that can be assembled more effectively and at a higher quality.
Examples of this design strategy have seen processes adapted to ensure a product can be assembled by robot to limit risk of waste material. Launching design with automation allows a faster ramp-up to volume if demand increases faster than expected, with significantly less waste and redundancy implementation for multiple assembly lines.
Design for Longevity
Great engineering design starts with careful consideration of the product requirements up front. Sustainability and the impact of a product can, and must, be considered at every stage.
Considering the end of life or aftermarket of a product is also a key element of designing for cost. Accommodating and adding value to the end of product life can only improve the design. For instance, aftermarket services make ‘recycling’ devices possible as parts and materials can be reclaimed, limiting the end-of-life impact of the equipment and supporting sustainability objectives.
Supply chain, cost and automation all play a part in the final design. Choices made in each of these areas, at every stage of design, can improve the sustainability of a final product. A good design partner can help ensure a product takes every area of impact into account, creating the right product, at the right price, with sustainability challenges taken into account at every point in a products lifecycle.
Peter Smith engages Plexus customers on product development projects in different sectors. He came to Plexus with 10 years of medical device product development experience at specializing in electrosurgical, microwave systems including the regulatory planning and approval process for CE MDR, 510k and PMA. He holds a Ph.D. and an M.Eng. for Electrical and Electronic Engineering from Heriot-Watt University, Edinburgh. He is a Chartered Engineer with the UK Institute of Engineering and Technology.