The Reading Room – September 2021
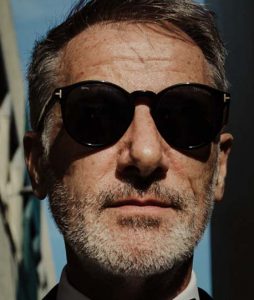
By Philip Spagnoli Stoten Founder of SCOOP
As we exit September it is becoming increasingly clear that all isn’t as it should be with the world. Here in Australia COVID-19 case numbers are rising quickly, vaccine rates more slowly, and lockdown is set to continue for at least another month. Elsewhere many countries are living with COVID and the associated hospitalisations and tragic deaths are now becoming the norm. Meanwhile the manufacturing and supply chain world is dealing with yet another major disruption.
For manufacturers the shortages of components are causing multiple challenges from the simple fact that some products cannot be completed and shipped to rising costs that can’t always be passed on to customers. Problems in the supply chain are manifesting in numerous ways, from container ships queued at ports to 10x increases in transport costs. All in this is challenging revenue, growth and, of course, cash flow.
At SCOOP we love to ask the big questions and try to dig deep with those in the front line to understand the what, why, when and how. Having reached out to numerous executives for comment we published a What’s the SCOOP – Component Shortages Special in EMSNOW with comments from ten of the world’s leading EMS CEOs and another ten movers and shakers in the industry.
This week I talked to IPC Chief Economist Shawn DuBravac on the same topic who, armed with solid research, told me that the two biggest challenges facing the industry are shortages in the supply chain and shortages in available talent, two issues that are not going to be fixed quickly. For those that haven’t seen the interview I have embedded it below as both video and podcast.
The same topic of shortages also took up some airtime on a panel discussion I was pleased to be invited to participate in last week hosted by the wonderfully charismatic Mike Konrad and with guests from the media, including Mike Buetow, Trevor Galbraith and the ever charming Eric Miscoll. There were plenty of other topics discussed that make this video and podcast well worth a look and listen. Also embedded below.
So, what else is going on in the world of manufacturing and supply chain, I hear you ask?
- Ford to build new plants in Tennessee, Kentucky in $11 billion investment in electric vehicles. Ford had already announced an investment over the past two years of $950 million in the Rouge Complex in Dearborn, Michigan, to build the all-electric 2022 F-150 Lightning. Bringing the battery supply chain to the U.S. insulates Ford from being held hostage by battery shortages the way the industry has been kneecapped by the global semiconductor chip shortage.
- Elsewhere in the automotive sector, Customer-Bound Electric Lucid Air Sedans Now Rolling Off Assembly Line, according to Forbes. Lucid has now completed all government certifications for the Air including an EPA estimated range of as much as 520 miles. The first customers of the Air Dream Edition will start getting their cars in late October and Lucid has increased the production run for this variant to 520 units, matching the range number.
- Ethan Karp of Forbes asked MIT Researcher Ben Armstrong, “Have We Been Approaching The Skills Gap In Manufacturing All Wrong?” Ben Armstrong has his finger on the pulse of U.S. manufacturing. That’s what happens when your research has you talking with dozens of manufacturers across America to understand their struggles and successes and how we might address the industry’s long-simmering deficits in skilled labor, technology and training.
- And according to Sophie Mellor in Fortune, at “three months before Christmas, companies are already bracing for stock shortages and bonkers prices”. Retailers like to say that Black Friday is so named because the holiday buying frenzy that comes the day after Thanksgiving is when they move into the black—or begin to turn a profit on the year. But in the upside-down world of the COVID-19 pandemic, it may be the day when many of them sink into red ink.