Qualitel Describes Inspection Partner, Koh Young, as Essential to Sustained Growth

By Brent A. Fischthal, Koh Young America
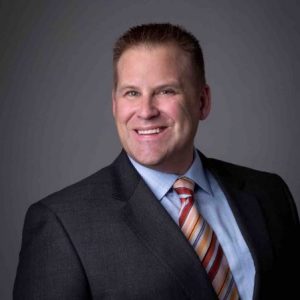
Brent A. Fischthal
Celebrating a quarter of a century this year, Qualitel operates a 71,000 sq. ft. EMS (Electronics Manufacturing Services) facility with state-of-the-art equipment dedicated to building complex, high reliability printed circuit board and turnkey assemblies. Qualitel is ITAR registered, aligned to NIST 800-53 with certifications that include ISO9001/AS9100 and ISO13485.
Specializing in manufacturing electronics with complex SMT (Surface Mount Technology), BGA (Ball Grid Array), and fine pitch technology for the aerospace, medical, life sciences, industrial, and military markets, Qualitel is located 20 miles north of Seattle, Washington, close to Paine Field International Airport.
With more than 200 employees, Qualitel offers both production manufacturing and prototype services, which they refer to as Qualitel Corporate and Qualitel Express, respectively. Each facility has its own state-of-the-art manufacturing of equipment and dedicated teams.
From prototype to production, Qualitel’s operations and business model is designed to be flexible and responsive to customers, while meeting their strict quality requirements. Qualitel’s customers include public and private aerospace, medical, and other mission-critical companies that rely on the capabilities and expertise they provide.
An Ambitious and Demanding EMS
Qualitel applies their core values of Responsiveness, Reliability, Respect, Teamwork, and Cares to their team, as well as their suppliers, customers, and the products they build. Qualitel continues to be the supplier of choice for OEMs (Original Equipment Manufacturers) seeking a partner specializing in a full range of high-mix, medium-low volume manufacturing of high-reliability products where “failure is not an option.”
Qualitel bakes quality into everything they do – every project, every product, and every process. So, when they decided to invest in 3D SPI (Solder Paste Inspection) and 3D AOI (Automatic Optical Inspection), they knew ‘baked in quality’ was essential. They were looking for real-time, in-line inspection solutions that could provide closed-loop feedback to ensure quality was built into the product. They needed more than just a “go/no-go” feedback.
And that wasn’t all that was on their shopping list. They were looking for a solution that was easy to use and fast to program, plus it had to be accurate and reliable with a very low false call rate. It also needed to connect to their AEGIS SPC traceability system.
“Koh Young’s initial presentation was very clear and detailed; highlighting all the capabilities, ease of use in programming and functionality that we felt it was only right to add them to our assessment. They also invited our team to their demonstration facility to walk through an evaluation run. After a short time period, this was an easy decision to engage in contract negotiation and scrap our current supplier that we were evaluating in-house… Koh Young’s capabilities far exceeded the competitors and we are very happy with our decision.” Hoa Hoang, Qualitel’s Vice President of Operations
Qualitel selected Koh Young for many reasons, from their worldwide presence and reputation for continuous improvement through the accuracy of their data, the ease and speed of machine programming, to their conversion support and simplified images and data.
Qualitel started with two SPI machines and four AOI machines. Koh Young’s technical support was onsite to train Qualitel engineers and support the machine handover. As with any change, the operators were initially hesitant, but after the machines proved their speed and dramatically reduced false calls, there was a complete mind shift. They quickly accepted and adapted to the new machines.
Immediate and Dramatic Performance Improvements
After a short while running the machines, Qualitel realized immediate benefits, including:
- 95% reduction in false calls
- Reduced production time
by 2.5 minutes per assembly
- Reduced production time
- 75% reduction in programming time
- Upgraded inspection parameters, such as:
- IPC-A-610-based Joint Measurement
- Lifted Leads and Parts
- FOD (Foreign Object Debris)
- Component lead & body Coplanarity
- Reduced product rework
- Improved first pass yield quality
- 50% DPMO improvement
- Dramatically improved downstream
test yield to over 98% - Improved solder paste print accuracy with
new inline 3D SPI inspection technology - Simplified data collection effort to
monitor and control process limits
And There’s More to Come
Qualitel’s journey and partnership with Koh Young continues as they explore automated optical inspection in post-SMT processes. Qualitel has been satisfied and impressed with the selection of Koh Young. They have become a trusted partner.
“Koh Young is a trusted, extremely responsive partner of Qualitel. We look to them for assistance in multiple areas, including process questions, application support, and software updates. We reach out to Koh Young whenever we need technical support, and they are there for us. We added Koh Young at a time when we needed to triple our output. They fully supported our implementation, without which would have stalled our rapid growth. Koh Young is essential to Qualitel and we would confidently recommend them to anyone!” Hoa Hoang, Qualitel’s Vice President of Operations
Qualitel uses Koh Young 8030 Series Solder Paste Inspection (SPI) and Zenith Series Automated Optical Inspection (AOI) solutions. For more information about the Koh Young SPI and AOI visit kohyoung.com.